The Logistics Company (TLC)"Logistics Planning Project Idea
Background and Justification
The Logistics Company (TLC) has been generating international logistics plans for its clients since 1979. This process includes generating sourcing and transportation plans. Though we have been successful, the inefficiencies in our current processes limit our number of clients.
Though some aspects of our current process are automated (warehouse inventories, shipment packing plans, etc.), we lack an end"to"end automated process. We feel that having an end"to"end automated process would greatly decrease the time required to generate our logistics plans and would therefore allow us to increase our client volume and grow our client base.
Current Business Process
This "international logistics planning" process is highlighted in more details below:
Customers submit orders for one of our client"company's products to TLC for logistics planning/processing. TLC works out the optimal logistics plan. Customer orders contain one or more line items (an entry in an order that details the product and quantity).
For each line item in an order:
o Find all warehouses with the product in stock
" Warehouses contain products in "packs." The product describes the details of what the product is ("Kenworth A210 Drive Wheel Axle," "Hydraulic Cylinder Assembly," SD400 Forklift Chassis," etc.). The pack is the standard shipping unit for the item (e.g., "Hydraulic Cylinder Assembly" ships in a two"pack). Packs are "real" things"they have a location, manufacture date, etc.
o Select the best warehouse(s) with ordered product(s)
" Users can specify a warehouse order"of"preference to indicate how to select a warehouse when multiple warehouses have a requested item in stock.
" Products are removed from warehouse inventories using an oldest"item"first scheme"oldest products (by manufacture date) are taken from inventories before newer ones.
" When sourced, packs are packaged into large shipping containers. Shipping containers are the basic shipping element used by TLC (i.e., TLC ships containers full of packs, not individual packs).
o Determine best path from warehouse(s) to destination based upon the order's priority.
" Orders can be processed via two possible priorities:
Time"Best paths from warehouse to destination are chosen based upon fastest delivery time (regardless of cost)
Cost"Best paths from warehouse to destination are chosen based upon lowest cost (regardless of time). Costs include the cost of containers,
o Book the time at the selected facilities (warehouses, air, and seaports) and allocate the needed containers, and reserve time/space on the appropriate transportation mechanisms (trucks, ships, aircraft, etc.)
" All facilities have a booking schedule"As a facility becomes more "booked" they become a less attractive sourcing option due to the increasing delays involved.
" All transportation mechanisms have a booking schedule"As they become more booked "they become unavailable.
The main outputs of this process are packing plans, schedules, and manifests.
o The packing plans indicate what packs of what products go into what container (this is designed to maximize container utilization). For example:
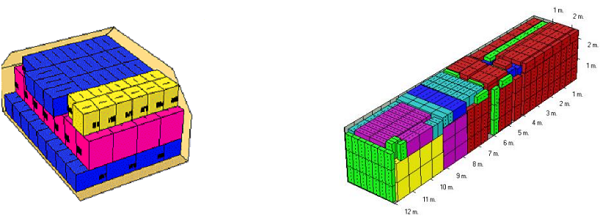
o The schedules indicate which facilities are booked when (warehouses, sea/airport loading facilities, etc.), and for how long:
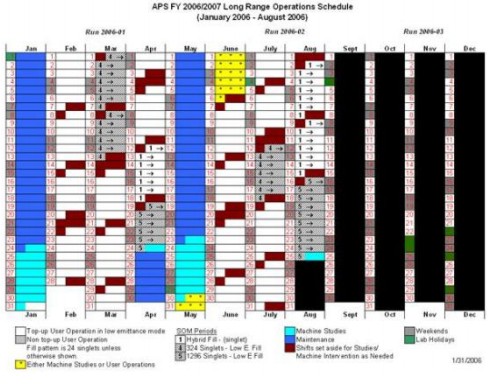
o The manifests indicate what individual product"packs are to be loaded into which containers and which containers are loaded into which shops/aircraft.
Logistics Planning Flow Diagram:
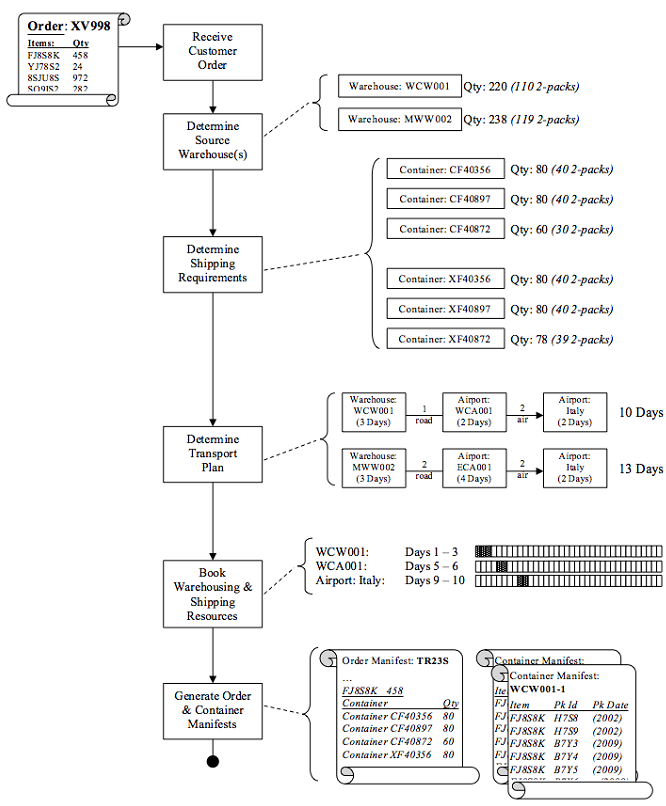
Order Processing Example Flow:
For each order line item (product and quantity), find all warehouses with this product in their inventory.
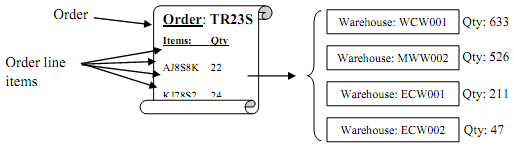
Once the warehouses with this product in their inventory have been determined, allocate the items from the warehouse(s) following a user"specified order of warehouse preference until the requested quantity is met or the supply of the product is exhausted. Products should be sourced from a single warehouse if possible (i.e., not split one order item across multiple warehouses) unless the requested quantity cannot be sourced from only one warehouse.
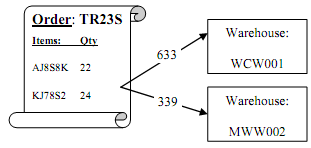
o Remove the products from the warehouse's inventory.
o At each of the selected warehouse(s), the packs of the desired product should be packed into shipping containers.
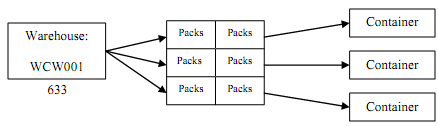
Next, determine all possible paths from the source warehouse(s) to the destination (some might not make sense). This includes determining the processing time at each facility, the travel time between points, and any delays if the warehouse time is unavailable (e.g., the warehouse is already booked on a certain day).
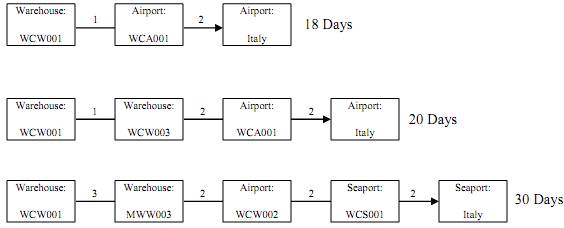
o There can be many, many (thousands of) possible source paths.
o From all these possible paths from each source warehouse(s) to the destination, select the optimal path based upon priority (cost/ time). These will be the selected "Source Paths.
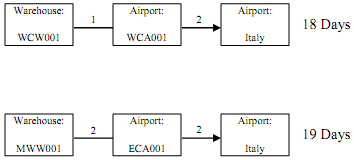
Then, "book" the needed time at the facilities involved in the selected source paths.
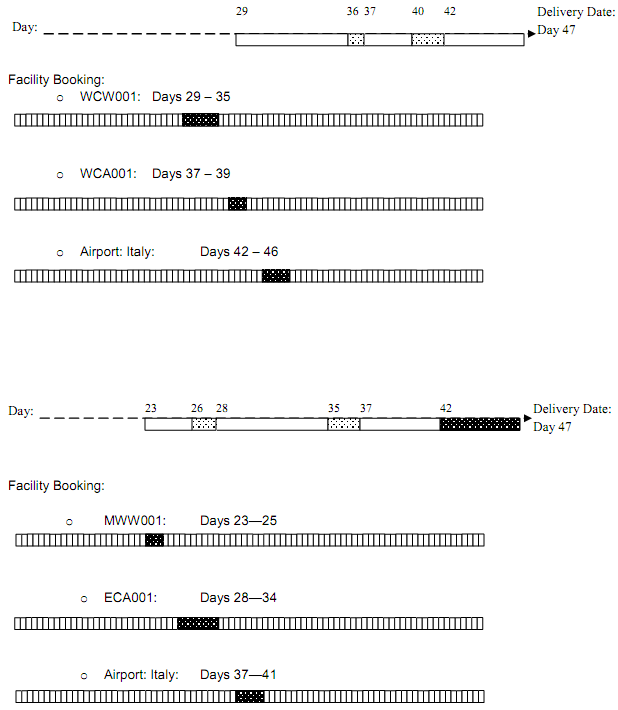
Add all sourcing information to the order manifests, container manifests, etc.
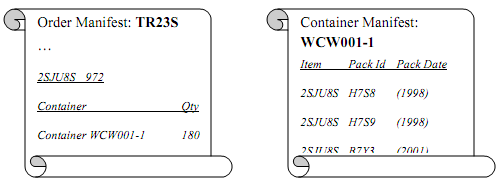
Continue with remaining order items.
Known Issues
The major outputs for this new system are to be the same as the current manual system" container/ship/aircraft packing plans, schedules, and manifests.
Our internal database contains all needed details on all products a user can order.
The warehouses each have a computerized inventory system that allows quick look up and allocation of warehouse assets and also handles the booking of warehousing time. Though all warehouses use this system, they run independently and do not communicate to the "outside world." This project needs to include work to expose the warehousing systems to the "outside world" so that our new system can communicate with the warehouses.
We deal with all container allocations within the company already, so no external input is needed. However, this process is currently a manual process.
We already use Internet"based applications to book air/seaport time and ship/aircraft time. The new application should simply work with these existing applications.
We have no existing hardware to develop and run the new system, so hardware/software acquisition is to be considered part of this project.
We have two software developers (Java programmers) and one software tester on staff that can be made available for this project. Any additional resources will need to be acquired as consultants. The determination of additional staffing and the process of acquiring that staff is to be considered part of this project.
We expect the new system to be able to develop a logistics plan for an order in less than one minute. All container/ship/aircraft packing plans, schedules, and manifests must be complete, consistent, and accurate.
Costs and Time Table
If this project is approved, the application must be completed within 120 days. Additionally, functional demonstrations are to be presented to the project stakeholders every 30 days.
The cost of developing this application will be determined in the initial project planning stages.