Question 1
Design a surface blast for the following conditions:
a) Ore of density 2.7 tonnes/m3
b) Grade control blast, also known as a paddock blast
c) Tonnage to be blasted 540,000 tonnes
d) Bench height 10m
e) Blasted length 200m
f) Blasted width 100m
g) Assume wet rock conditions
h) Conductive ore so Nonel initiation to be used
As part of the design, select an appropriate hole diameter and drill rig, design the blast and initiation pattern. Also hole loading and primining must be considered.
Question 2
Design a coal overburden throw/cast blast for the following situation:
a) Blast length 400 m
b) Blasted bench width 100 m
c) Bench height 30 m
d) Overburden of shale/siltstone/sandy shale, average density 2.5 tonnes/m3
e) Standoff distance 1.5 m
f) Dry conditions
g) Hole diameter 250 mm
Design the blast pattern, select initiation system, detail initiation sequence.
Question 3
A surface mine blasting operation has been designed utilising 100 mm diameter holes to blast granite with 10m long holes, using an explosive with a powder factor of 0.6 kg/m3 and a density of 1100 kg/m3. Stemming length is 2 m. The blast is 100 m long along the bench and the bench width is 30 m. For granite assume k = 25. Determine the maximum throw length for both bench face and cratering fly rock and provide a sketch detailing maximum throw length and the clearance distances for equipment and personnel for this blast.
Question 4
Design a tunnel blast for the following situation:
a) Blasting a 5.5 m by 5.5 m tunnel in sandstone
b) Hole length drilled is 4 m
c) Blast hole diameter is 75 mm
d) In the cut area 3 holes are drilled and left uncharged these holes are also 75 mm in diameter
e) A burn cut is to be employed
f) Wet rock conditions
g) Perimeter blasting techniques are not used
Design a suitable blast pattern, select suitable initiators and detail the initiation pattern.
Question 5
Design a suitable blast for the sub-level caving arrangement shown below which is from Kiruna Mine. In particular emphasis should be places on selecting an explosive of a suitable powder factor, initiation and determining the spacing of the blast hole pattern. Note sub level caving involves constrained blasting conditions, solid rock is blasted into broken rock so maximum void ratio will be 18% to account for the swell.
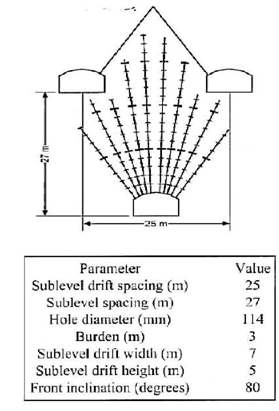